Services
Some of the Ways We Help Our Customers
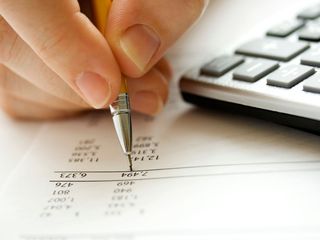
Six Sigma Process Improvement
Six Sigma is an extremely effective methodology for improving the performance of an organization by minimizing product or service defects. It recognizes that there is a "cost" associated with every error that is committed. This may range in seriousness from having to redo a task, replace a part, waste time or materials, reduce efficiency, or even lose a customer.
Learn More
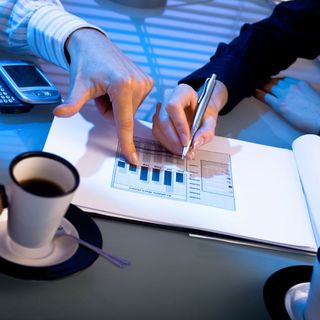
Design for Six Sigma (DFSS)
The purpose of DFSS is to avoid manufacturing- or service-related process problems by using techniques , tools, and processes to simulate the product delivery system, incorporate the needs of the customer, consider engineering system parameters, and predict issues before they occur. This helps ensure products and services provide greater customer satisfaction and increased marketshare.
Learn More
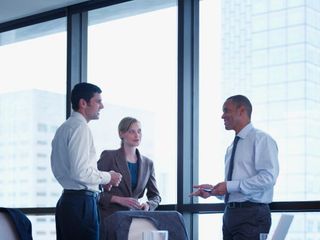
Critical to Quality (CTQ) Implementation
An important part of Six Sigma, CTQ is used to define quality features or characteristics that are important to the customer. The process of developing a CTQ flowchart also helps identify problems and their root causes.
Learn More
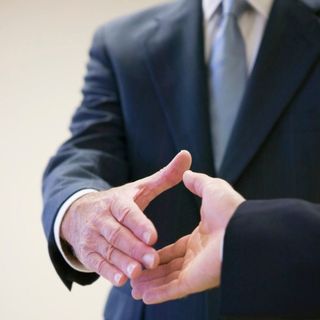
Voice of the Customer (VoC)
An important aspect of business strategy, especially in an age where customers demand direct engagement, VoC captures customer feedback about experiences with and expectations for a company's products or services. It defines customer needs, expectations, and understandings, and helps point to areas requiring product improvement.
Learn More
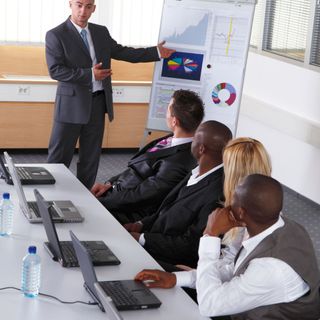
New Product Introduction (NPI)
Developing and introducing new products is costly and time-intensive. The NPI process helps streamline innovation by ensuring all activities used to define, develop, and launch a new or improved product are carefully planned, evaluated, and adjusted where needed to improve return on investment.
Learn More
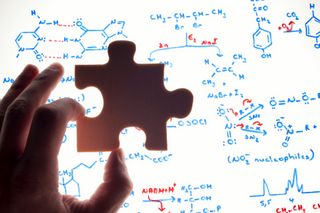
Stage-Gate Methodology
The Stage-Gate method of product development involves defining the business case, assessing its feasibility, doing design followed by design development, reviewing pre-launch plans and documentation -- including marketing, and finally completing launch and evaluating deliverables.
Learn More
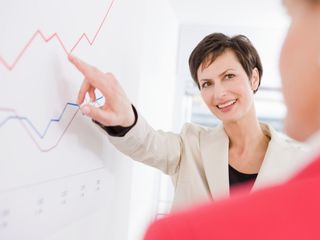
R&D within an Open Innovation Environment
For organizations utilizing open innovation for R&D, it is important to optimize the technology portfolio to ensure it will meet a company's needs today, tomorrow, and in the future.
Learn More
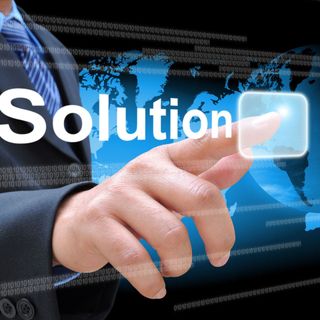
Roadmaps/ R&D Transformations
An important aspect of long-term R&D planning is to evaluate the innovation pipeline to ensure it has sufficient product to meet not only today's needs but a horizon portfolio for the next 3-5 years. When found to be insufficient, a regional or even global R&D transformation and product development process needs to be implemented. A technology roadmap is a good place to start.
Learn More
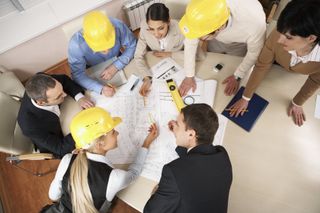
Certification & Validation Processes
Companies often need help with vital industry certifications and validations -- including design for manufacture & assembly (DFMA), advanced product quality planning (APQP), or help obtaining certifications from Underwriters Laboratories (UL) or the US Food & Drug Administration (FDA).
Learn More